LEAN PROCESSES, LLC
Processes for Greater Productivity · Practical · Proven · Profitable Solutions

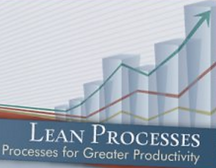
Lean Tools Training
More Than Just Training
Practical Training and Implementation You Can Use
We believe in experiential learning, so our training is always interactive and hands on, not just lecture. Training is always intended to be practical, useful and relevant to your business, not just ivory tower ideals. We prefer training to be a part a facilitated improvement event, so that the training will be put to practical use.
​
While there are a variety of tools that can be impactful to your business, there are a handful of tools that businesses trying to start a Lean implementation, or trying to re-invigorate their Lean efforts will typically deploy first. The following tools represent the most common starting points, but does not reflect the complete offerings. Let us know if you have interest in a topic you don't see listed here. We would love to help.
The quick summary:
​
Lean Tools Training
-
Not just lecture
-
Hands on, interactive
-
Simulations to improve understanding
-
Practical training you can use
Tools such as:
-
5S
-
8 Wastes Training
-
Setup Reduction / SMED
-
Training Within Industry (TWI)
Simulation - Large group hands on exercise demonstrating many Lean concepts all at once
What can typically be expected?
​
Lean Tools Training
-
2-4 hours of training
-
Implementation within faciliated improvement event
-
Participants from variety of departments to participate and contribute
Common Results
-
5S - commonly 20% reduction in process time
-
Setup Reduction / SMED - commonly 50% reduction in setup time
-
Training Within Industry (TWI) - commonly 50% reduced overall training time with fewer quality variances
5S - One of the most basic Lean tools. Roughly translated from 5 Japanese terms starting with the letter "S" they are most commonly translated to:
-
Sort - the act of sorting out what items are used and with what frequency
-
Shine (cleaning up the area and contents within and repairing tools or machinery being used
-
Set in Order - the strategic placement of items back into the work area in the most efficient manner currently realized
-
Standardize - the standardization of the work area to elminate variances in the process and between workers
-
Sustain - the process put in place to help everyone who works in the area to be able to return the area back to its intended state for the next person. This simple process should be included (at least informally) within any process improvement activities
8 Wastes Training - the foundation for all Lean activities. You can't minimize waste if you can't identify and understand it. There are 8 widely accepted categories of waste. This training is intended to help participants understand what they are, learn to identify them and serves as the foundation for all Lean activities since the primary focus of all Lean activities is to reduce or eliminate waste. The concepts taught here will be constantly revisited and reused in all other activities and is pivotal to being able to implement Lean and realize sustainable gains.
​
Setup Reduction / SMED - this training is intended to demonstrate and instruct the concept of setup reduction through the identification and separation of Internal and External activities, the conversion of internal to external activities and ultimately the reduction of time spent in internal and external activities. This is instructed as a hands on demonstration that can be further demonstrated by its inclusion in the larger Lean simulation. This is reported as one of the most impactful and enjoyable training sessions based on participant feedback.
​
Training Within Industry / TWI - This is a 3 part series that was originally created during World War II for the rapid improvement of a new work force manufacturing new products quick, correctly, consistently and safely. The 3 parts are taught as Job Relations (JR), Job Instruction (JI) and Job Methods (JM). The Job Relations is intended to lay the foundation for creating good relations within the workplace and provides a systematic approach to problem solving in the workplace. The Job Instruction is intended to provide a systematic approach to instructing people how to perform new tasks. The Job Methods is intended to provide a systematic approach to breaking down an existing process, identifying the waste within that process and implementing the changes that will improve that process.
​
Simulation - Intended for large groups to introduce them to the concepts of Lean. All of the above mentioned tools are included within the large group simulation along with about a dozen other Lean tools and concepts. This fun, very interactive exercise differs from many other manufacturing Lean simulations as it includes the information interface between the front office and operations rather than just focusing on how Lean is applied to the workfloor. This works best for 15-20 people, but can be modified for other group sizes.
​
We at Lean Processes will not share, sell or otherwise distribute your contact information and will not send you unwanted offers (SPAM). We will respond to your inquiry promptly.